Old But Innovative
We have passed onto our business through 300 years of history since its foundation as Otsuka Sangyo group.
In early 1700s, Otsuka Sangyo started mosquito net business in Nagahama, Shiga where our headquarter is still located.
If we are the same as we were, Otsuka doesn’t even excist. Our innovatioin is based on our flexibility that changes from time to time.
(Pictures are for illustration purposes only.)
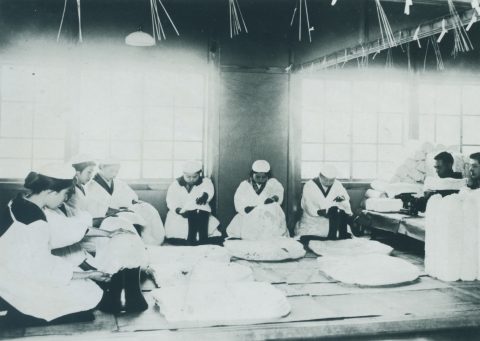
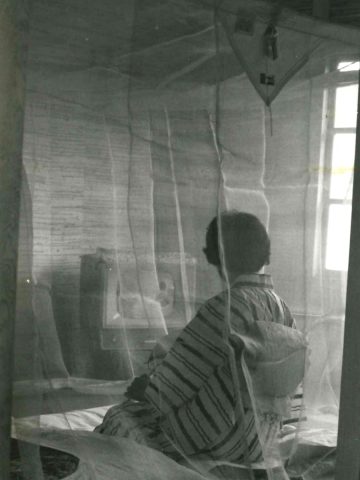
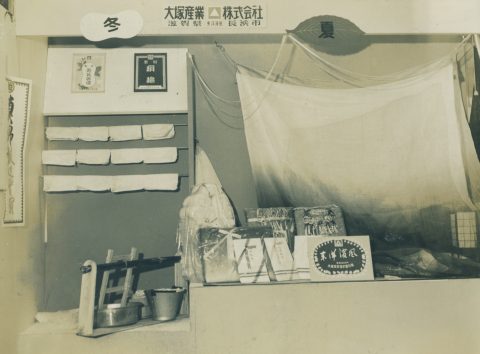
While demand for mosquito net was over the peak, we started producing wall paper for houses as the housing environment saw some changes.
Our fabric producing technology was smoothly applied to the needs for the housing market through our accumulated technology for mosquito net.
Then, by using our R&D capability, we became the designated wall paper supplier for Toyota housing of Toyota motor co. By doing so, the business was diversified to various housing makers, and the technology has been passed onto Otsuka Sangyo Interia. Co, one of our group companies.
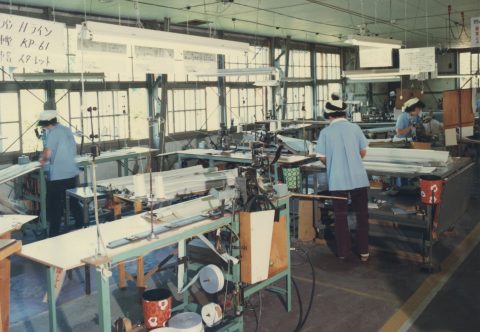
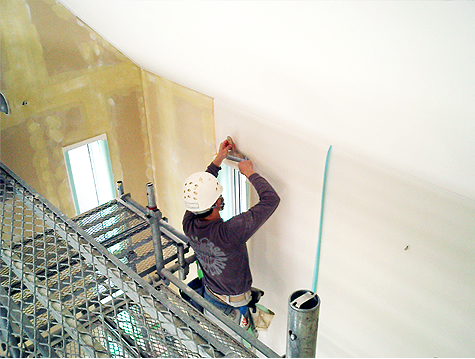
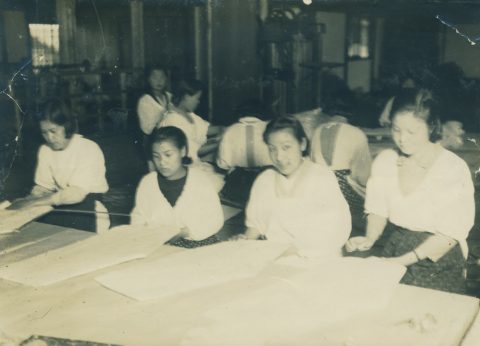
Our fabric technology became highly valued by Toyota Motors, which made it possible to start producing the seat cover and developping airbags.
In 1970, we started producing head linings (roof) for Toyota, then the business was developped into other automotive parts like supprt cloth for car seat and head rest covers. It was before the group was split.
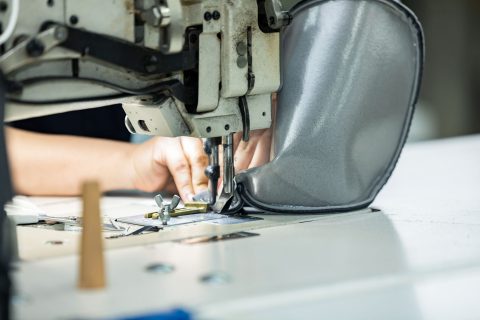
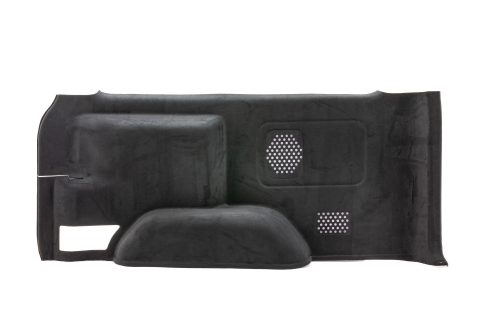
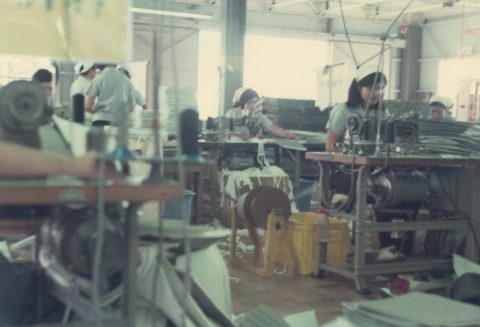
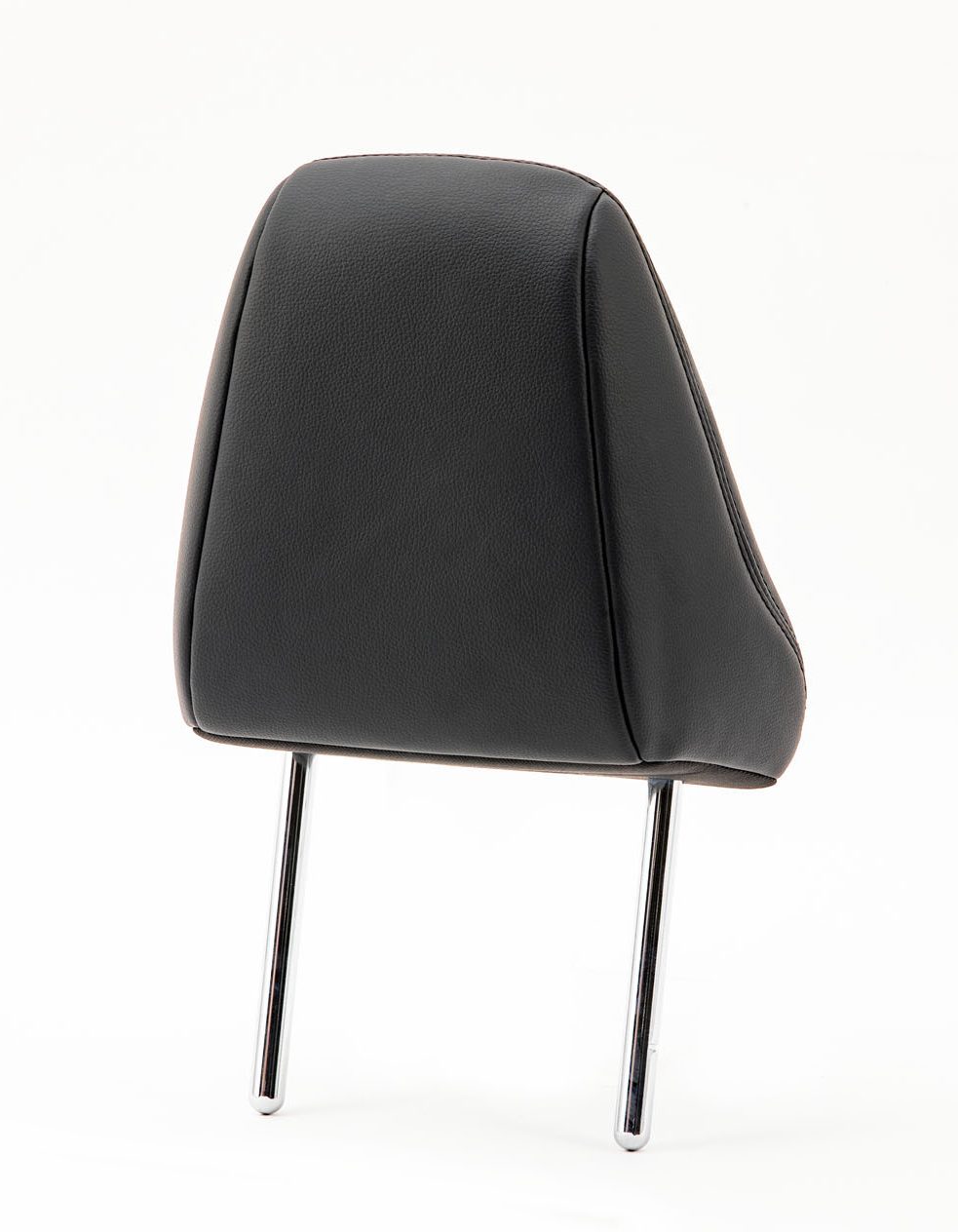
In 1987, Otsuka sangyo was splited into 4 companies, and Otsuka Sangyo Material was born that specialied in automotive business.
This is when Otsuka Sangyo Material’s innovaiton started.
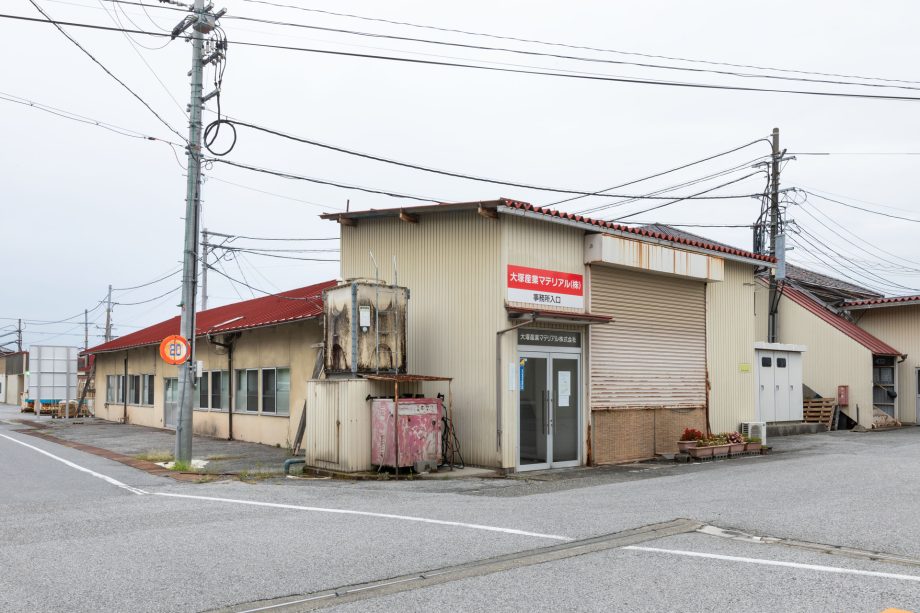

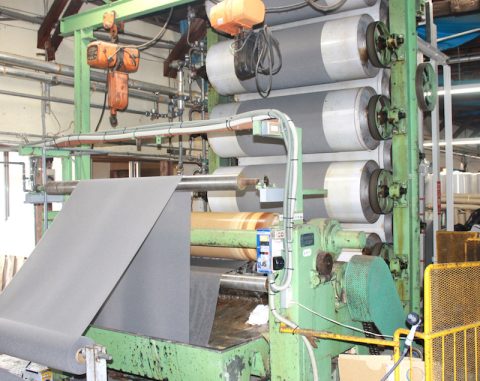
Not only headrest cover, we also manufacure supporting cloth for Poly Urethene pad for automobile cars by taking advantage of our long time accumulation of sawing technology.
The authodox method for supporting cloth was to cut a piece of fabric, saw it, and make it 3D shape for car seats.
However, cut and saw method reached its limitation when it came to recreating 3D shape. This was likely to end up losing market share.
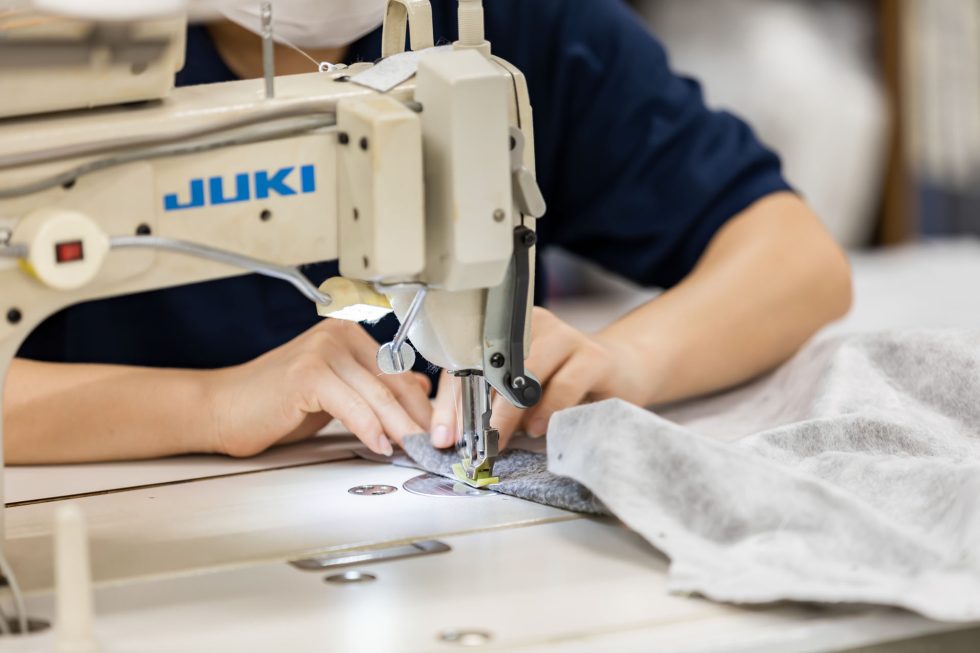
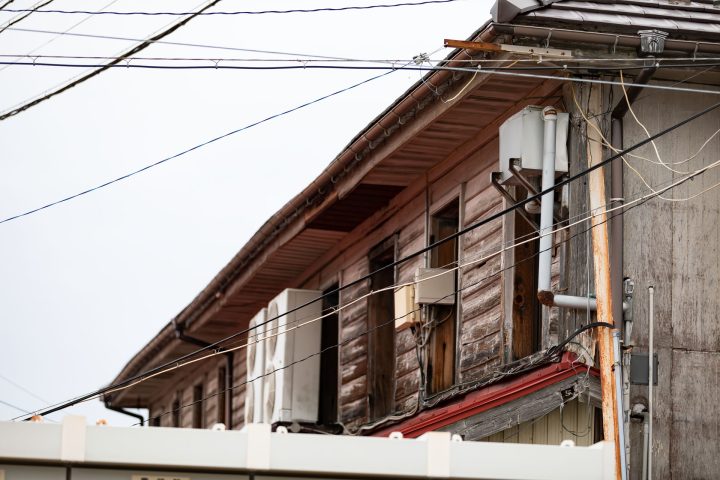
This is why we took a new challenge for molding technology of fabric.
In 2004, we introduced continuous molding machine and started developping producing prototypes by 3D-CAD at the developping phase.
This technology allowed a piece of fabric to be shaped into any complicated 3D shape.
Productivitiy and leadtime saw a huge improvement because of the continuous manufacturing system where raw material roll goes through in a continous manner unlike excisiting cut and saw technology.
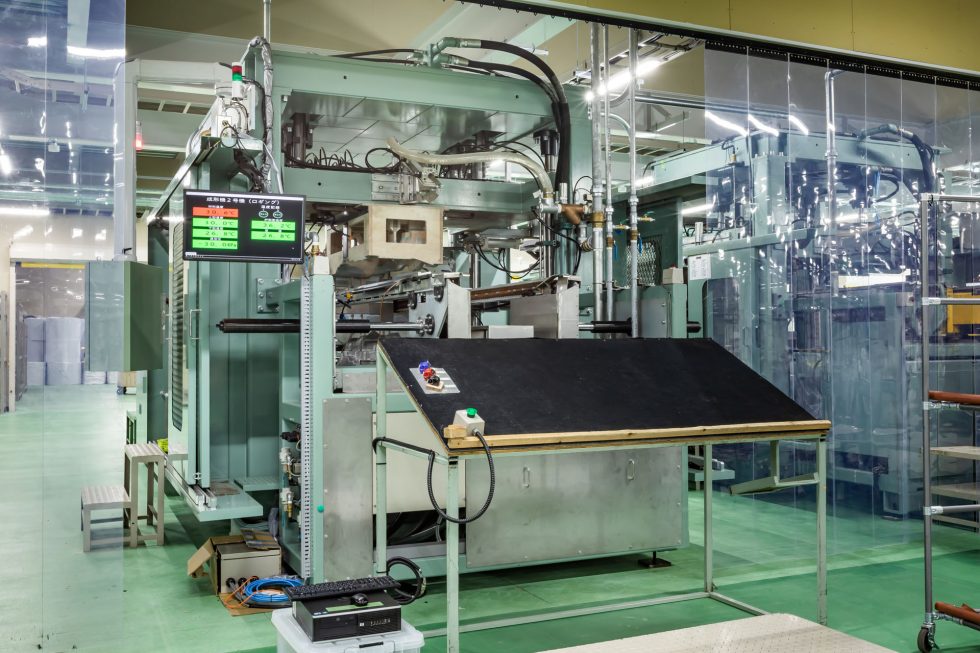
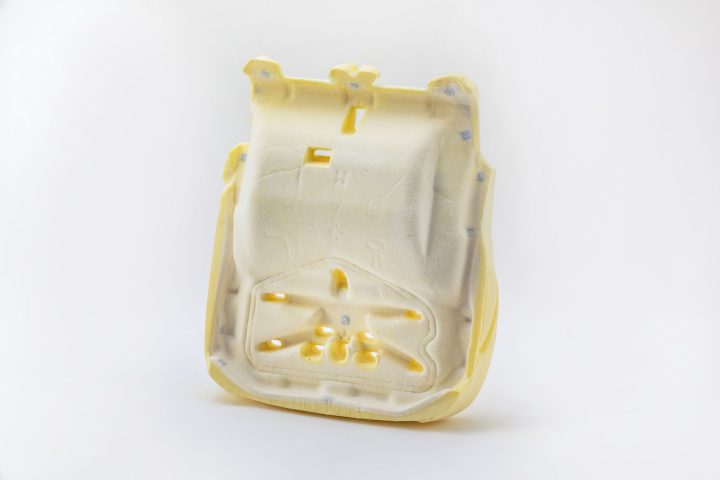
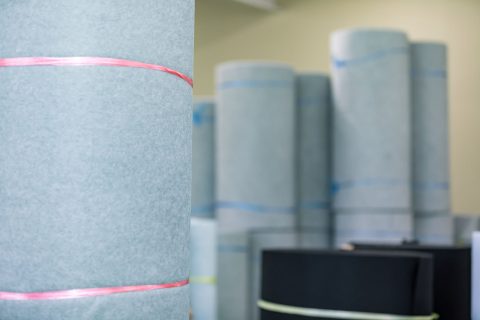
When it comes to the support fabric for urathane pad, you will see frequent design changes until mass production.
This is when our accumlated experience and knowleage come in handy to be able to give customers the proposal in advance. We have grown to exceed customers’ expectation.
Our proposal ability has been awarded such as Best Supplier Award, and we have about 70% of market share (according to our research)for cut/saw and molding products combined. These things have proved our accumulated proposal and technological ability.
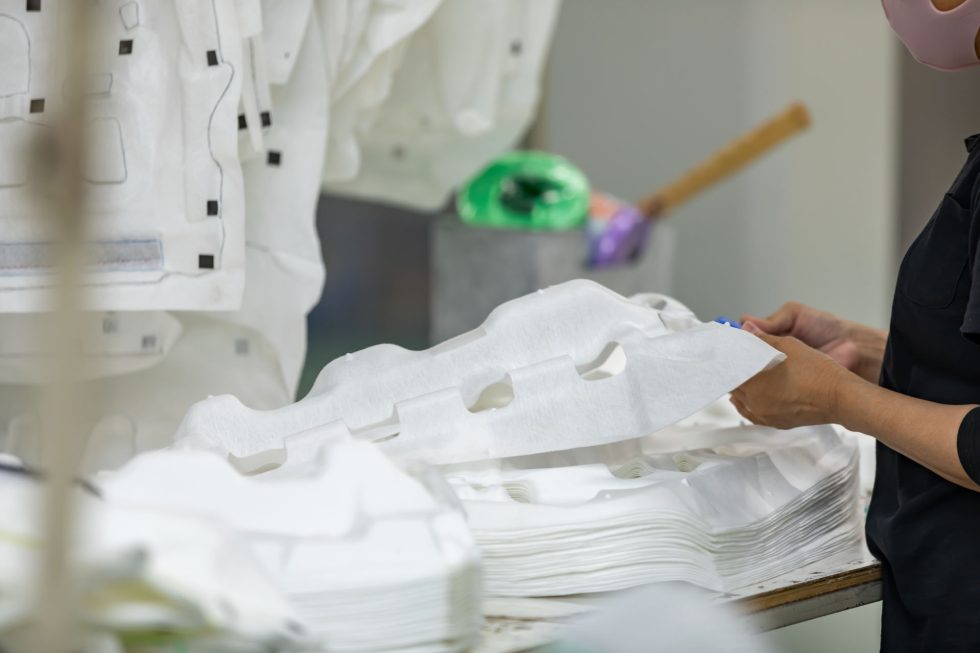
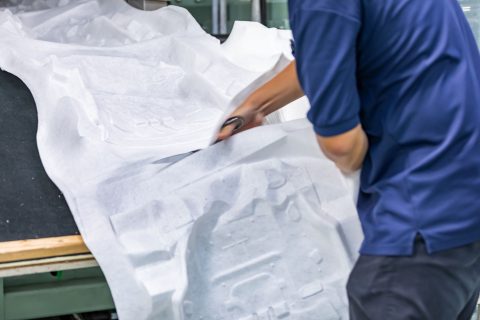
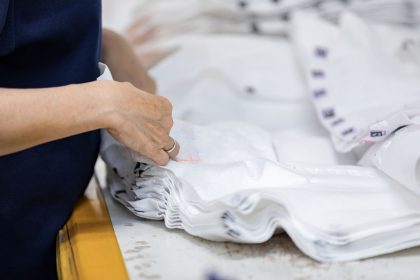
From there, we have diversified our business not only for automotive or non-woven fabric, but also for a wide range of products.
Our packaging products that is using felt materials such as non-woven fabrics has been highly recognized both domestically and internationally.
Speaking of environmental friendliness, some of our materials are consist of 50% of PET recyle material.
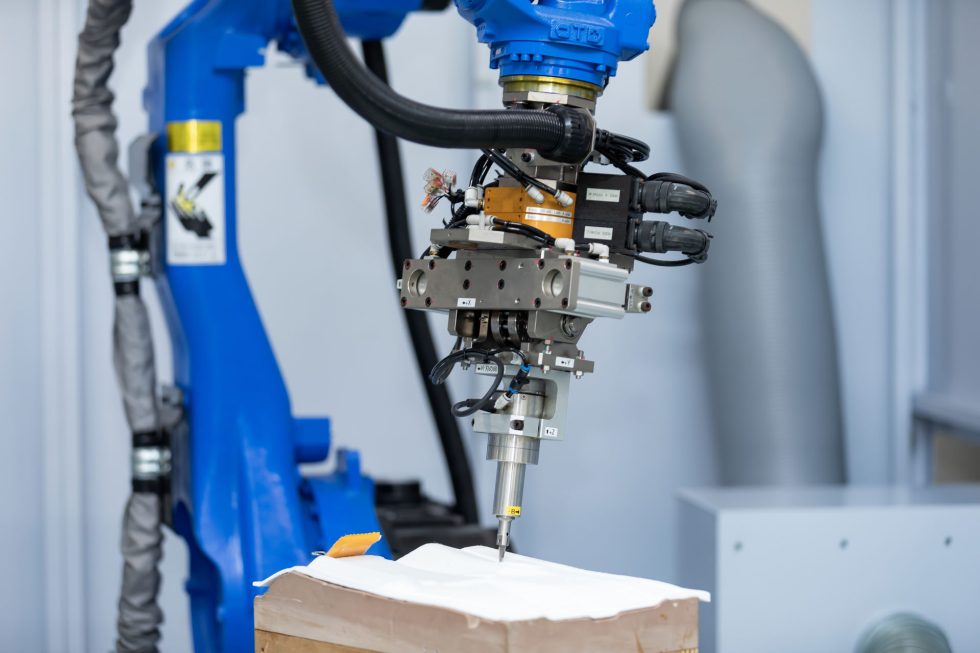
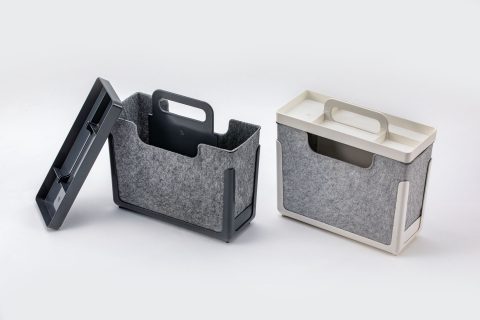
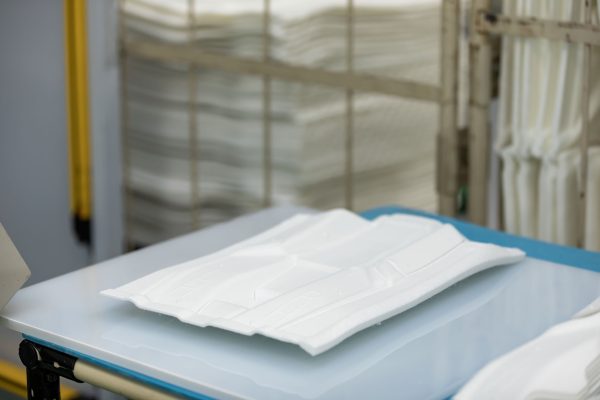
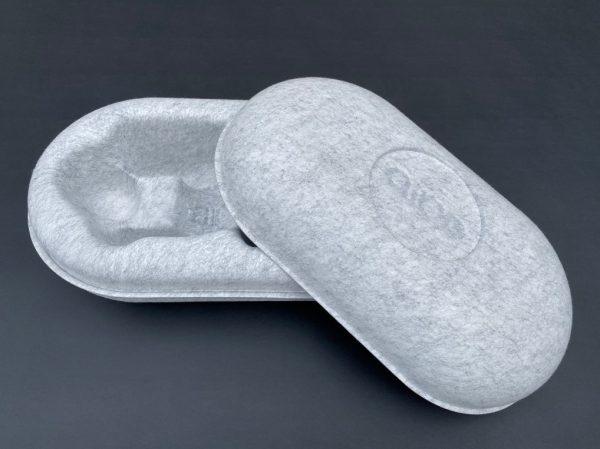
One of these that we do now is the molding foaming PE for heat insulation cover for fuel tank of Plug-in hybrid car (PHEV).
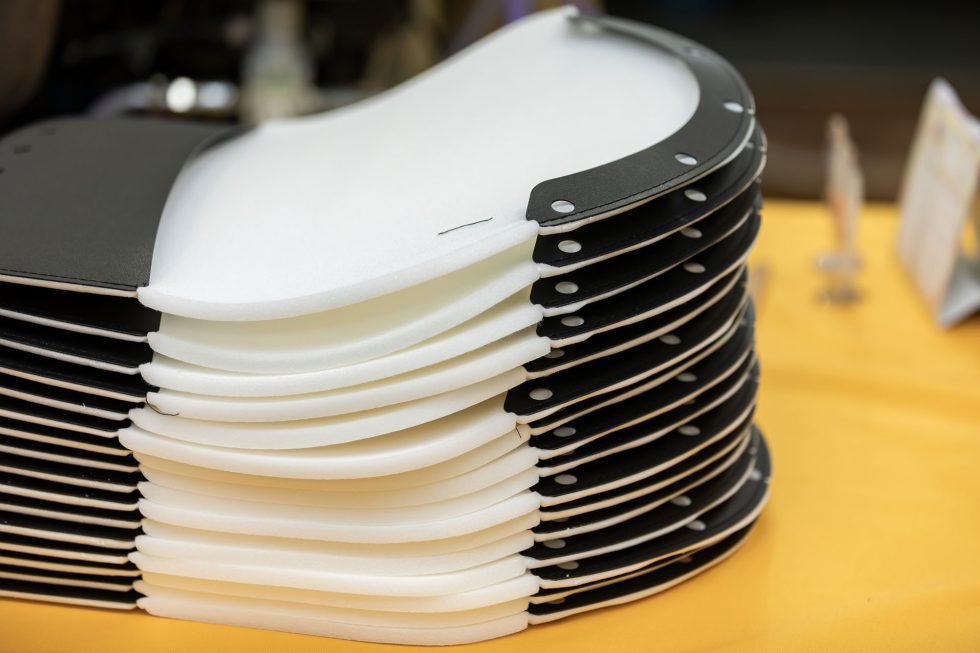
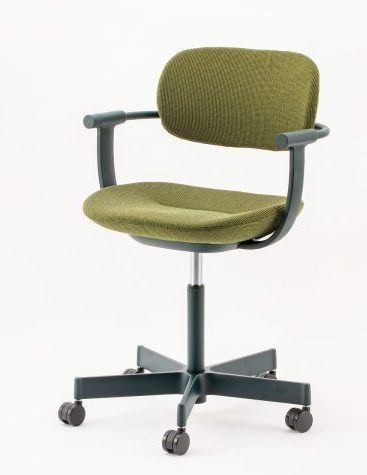
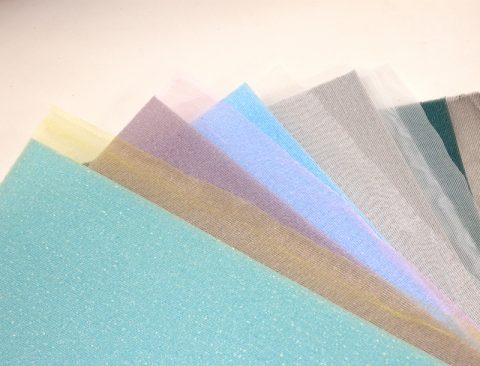
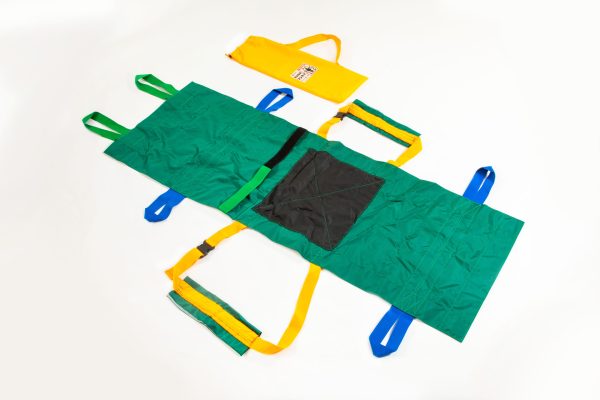
Besides that, we utilize the materials’ functionality like noise abosorption and biodegradability. Without destroying fanctionality, we are able to shape the material.
Another new technology we have been working on is so called water jet molding technology, which makes the state of fabric directly into the molding product. This is surely challenging, but we are expecting a lot to the innovative technology like this.
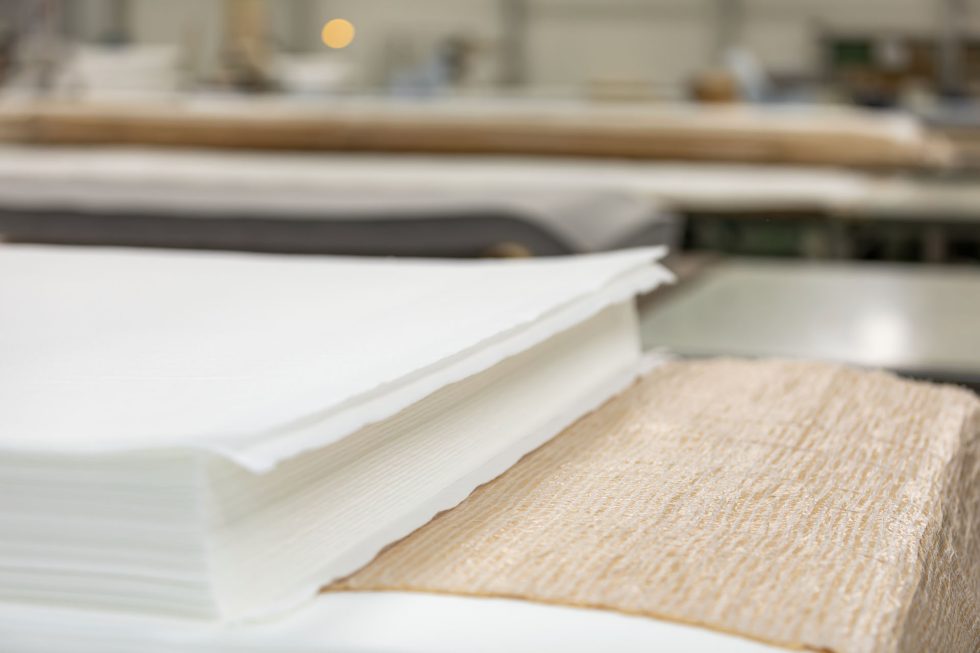
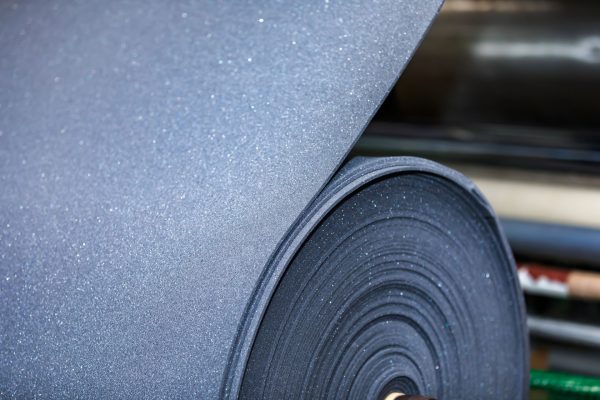
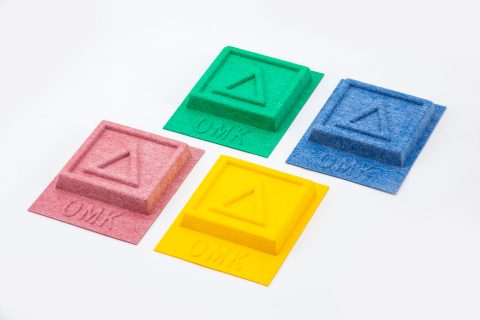
As we’ve seen so far, we have the long history of innovation. No company has the bright future without innovation. We strive to keep being innovative to meet the customers’ needs.
Let’s talk about our future. Not only our main business of automotive, we will diversify our business into other areas such as railways, office furniture, construction, civil engineering, medical care and nursing.
Moreover, we never forget to be innovative to create additional value.
Last but not least, in addition to “Sanpo-yoshi” spirit-great for 3 perspectives- , we have added 3 views of suppliers, the future, and the Earth, which makes it “Roppo-yoshi”- great for 6 perspectives-. With that in mind, we will try our best to create more values.
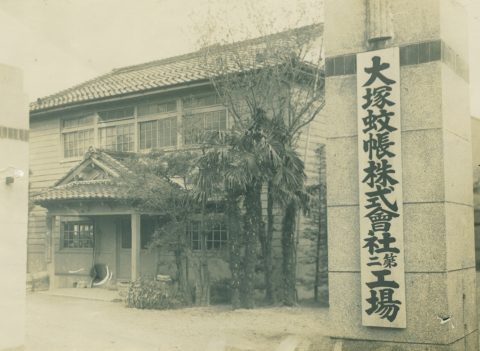
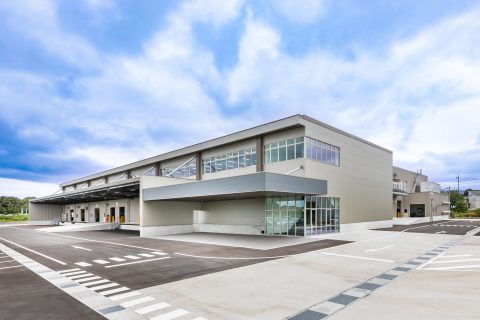